En omfattende veiledning om hvordan du setter opp et dreieverktøy
Å sette opp et skjæreverktøy for dreiebenk er en grunnleggende ferdighet for enhver maskinist, spesielt når du har å gjøre med dreiemaskiner med Computer Numerical Control (CNC). Riktig verktøyinnstilling er avgjørende for å oppnå presise og nøyaktige maskineringsresultater. I denne omfattende guiden vil vi fordype oss i de intrikate detaljene om hvordan du setter opp et dreieverktøy for CNC-skjæring. Fra det grunnleggende om dreiebenkverktøykomponenter til avanserte teknikker for å optimalisere skjæreytelsen, har denne artikkelen som mål å gi en omfattende forståelse av prosessen. Ved slutten av denne veiledningen vil du ha kunnskapen og ferdighetene som er nødvendige for å sette opp et dreiemaskinskjæreverktøy med selvtillit og presisjon, for å sikre optimale resultater i dine CNC-dreieoperasjoner.
Forstå skjæreverktøy for dreiebenk
I maskinens verden er dreieverktøy uunnværlige komponenter for å forme og transformere råmaterialer til presisjonskonstruerte deler. Enten du jobber med tradisjonelle manuelle dreiebenker eller avanserte CNC-dreiemaskiner, er det viktig å ha en grundig forståelse av dreieverktøy. I denne delen vil vi gå dypere inn i egenskapene, funksjonene og typene til dreieverktøy.
Egenskaper til dreiebenk-skjæreverktøy
Dreiebenk-skjæreverktøy er designet for å utføre en rekke maskineringsoperasjoner, for eksempel dreiing, flating, sporing, gjenging og mer. Disse verktøyene deler flere fellestrekk:
- Hardhet: Dreiebenk-skjæreverktøy er vanligvis laget av høyhastighetsstål (HSS), karbid eller andre spesialiserte verktøymaterialer. Disse materialene er valgt for deres hardhet, slik at verktøyet tåler de høye temperaturene og trykket som genereres under kutting.
- Skjærekant: Skjærekanten til et dreiebenkverktøy er den delen som faktisk fjerner materiale fra arbeidsstykket. Den er designet for å være skarp og presis, og geometrien til skjærekanten kan variere avhengig av den spesifikke oppgaven verktøyet er ment for.
- shank: Skaftet på dreiebenkverktøyet er delen som klemmes fast i verktøyholderen. Det gir stabilitet og stivhet til verktøyet under bearbeidingsprosess. Skaftdesign kan variere basert på type verktøy og produsentens spesifikasjoner.
- Verktøyholder: Verktøyholderen er en avgjørende komponent, spesielt ved CNC-dreiing, da den holder dreiebenken sikkert på plass. Den må gi stabilitet, presisjon og enkel justering for å sikre optimal verktøyytelse.
- geometri: Geometrien til skjæreverktøyet, inkludert skråvinkel, klaringsvinkel og sponknekker, spiller en betydelig rolle for å bestemme verktøyets ytelse. Riktig geometri er avgjørende for å oppnå effektiv materialfjerning og sponevakuering.
- Belegg: Mange dreiebenk-skjæreverktøy kommer med spesialiserte belegg, som TiN (Titanium Nitride) eller TiAlN (Titanium Aluminium Nitride), for å øke verktøyets levetid, redusere friksjon og forbedre ytelsen.
Funksjoner til skjæreverktøy for dreiebenk
Dreiebenk-skjæreverktøy utfører flere grunnleggende funksjoner i maskineringsprosessen:
- Materialfjerning: Den primære funksjonen til dreieverktøy er å fjerne materiale fra et arbeidsstykke. Denne fjerningen kan skje gjennom dreiing (rotering av arbeidsstykket mens du skjærer), vending (lage en flat overflate) eller andre operasjoner.
- Dimensjonskontroll: Skjæreverktøy er ansvarlig for å sikre at dimensjonene til den maskinerte delen samsvarer med de ønskede spesifikasjonene. Nøyaktig kontroll er avgjørende for å oppnå nøyaktige og konsistente resultater.
- Overflatebehandling: Kvaliteten på overflatefinishen bestemmes av skjæreverktøyets skarphet, geometri og skjæreparametrene som brukes. Et godt vedlikeholdt og riktig oppsatt skjæreverktøy bidrar til en jevn og fin overflatefinish.
- Chipkontroll: Effektiv sponkontroll er avgjørende for å forhindre sponoppbygging og opprettholde et rent og trygt arbeidsmiljø. Sponbryteren på enkelte verktøy hjelper til med å lette sponfjerning.
- Effektivitet: Dreiebenk-skjæreverktøy er designet for å gjøre maskineringsprosesser effektive og kostnadseffektive. De bidrar til å minimere materialavfall og optimalisere verktøyets levetid, og reduserer produksjonskostnadene.
Typer dreiebenk skjæreverktøy
Dreiebenk-skjæreverktøy er tilgjengelig i en rekke typer, hver skreddersydd for spesifikke maskineringsoppgaver. Her er noen vanlige typer:
- Dreieverktøy: Disse verktøyene er allsidige og brukes til sylindriske dreieoperasjoner. De kan forme de ytre og indre overflatene til et arbeidsstykke.
- Kjedelig verktøy: Boreverktøy brukes til å forstørre eller fullføre eksisterende hull. De er designet for presisjon og nøyaktighet i hullbearbeiding.
- Skilleverktøy: Skilleverktøy brukes til å skille et arbeidsstykke fra et større lager. De lager definerte skillelinjer med minimalt med avfall.
- Trådverktøy: Gjengeverktøy brukes til å kutte gjenger på et arbeidsstykke. De kommer i forskjellige former og størrelser for forskjellige gjengekrav.
- Rilleverktøy: Rilleverktøy lager riller eller utsparinger på et arbeidsstykke, vanligvis for å romme O-ringer, holderinger eller andre funksjoner.
- Verktøy for ansikt: Facingverktøy er designet for å lage flate overflater på enden av et arbeidsstykke. De brukes ofte for å oppnå vinkelrette overflater eller fjerne materiale fra en arbeidsstykkeende.
Å forstå egenskapene og funksjonene til dreieverktøy er avgjørende for å velge riktig verktøy for en spesifikk maskineringsoppgave. Valget av skjæreverktøy kan ha betydelig innvirkning på kvaliteten og effektiviteten til maskineringsprosessen, noe som gjør det til en kritisk avgjørelse i enhver dreiebenkoperasjon. I tillegg er riktig vedlikehold og verktøyoppsett avgjørende for å sikre konsistente og presise resultater, som vil bli diskutert mer detaljert senere i denne veiledningen.
Typer dreiebenk skjæreverktøy
Dreiebenk-skjæreverktøy kommer i forskjellige typer, hver spesifikt designet for en bestemt maskineringsoppgave. Å forstå disse forskjellige typene skjæreverktøy og deres applikasjoner er avgjørende for å velge riktig verktøy for en gitt jobb. Her er noen vanlige typer dreieverktøy:
Dreieverktøy:
- Rundneseverktøy: Brukes til generell dreieoperasjoner. Den har en avrundet skjærekant og er egnet for både grovbearbeiding og etterbehandling.
- Diamantverktøy: Oppkalt etter sin diamantformede skjærekant, er den ideell for presis bearbeiding på forskjellige materialer, inkludert metaller og plast.
- Square-Nose Tool: Har en firkantet skjærekant og brukes vanligvis til front- og skuldervending.
Kjedelig verktøy:Intern kjedelig bar: Brukes til å forstørre og etterbehandle eksisterende hull i et arbeidsstykke. Den er designet for presisjon og kan skape nøyaktige innvendige dimensjoner.
Skilleverktøy:Skilleblad: Disse verktøyene brukes til å kutte av et arbeidsstykke fra et større lager. De lager en definert skillelinje med minimalt med avfall.
Trådverktøy:
- Trådskjæringsverktøy: Designet for å lage utvendige gjenger på et arbeidsstykke. De kommer i forskjellige former og størrelser for forskjellige gjengekrav.
- Verktøy for trådjaging: Brukes til å jage eller gjenopprette eksisterende tråder. Disse verktøyene brukes ofte til gjengreparasjon.
Rilleverktøy:Rilleverktøy: Disse verktøyene lager spor eller utsparinger på et arbeidsstykke, ofte for å romme O-ringer, holderinger eller andre funksjoner.
Verktøy for ansikt:Facing Tool: Brukes til å lage flate overflater på enden av et arbeidsstykke. Det brukes ofte for å oppnå vinkelrette overflater eller fjerne materiale fra en arbeidsstykkeende.
Skille- og rilleverktøy:Kombinasjonsverktøy: Disse allsidige verktøyene er designet for både av- og rilleoperasjoner, noe som sparer tid og verktøyskift.
Gjenge- og rilleverktøy:Kombinert gjenge- og rilleverktøy: Ideell for jobber som krever både gjenging og sporing på samme arbeidsstykke.
Fasingsverktøy:Avfasingsverktøy: Brukes til å lage avfasninger eller fasede kanter på arbeidsstykket. Faser brukes ofte for å forbedre utseendet og lette monteringen av maskinerte deler.
Rølleverktøy:Rølleverktøy: Knurling er en prosess for å lage et teksturert mønster på et arbeidsstykke, vanligvis for forbedret grep eller estetikk. Rifleverktøy kommer i ulike mønstre og design.
Formingsverktøy:Skjemaverktøy: Disse verktøyene er spesialdesignet for spesifikke delgeometrier, ofte brukt til å produsere komplekse og ikke-standardiserte former.
Spesialverktøy:Profilverktøy: Brukes til å lage komplekse profiler på et arbeidsstykke.
Verktøy for vending og vending: Disse er designet for både front- og snuoperasjoner.
Avskjæringsverktøy: Designet for å skjære gjennom arbeidsstykket for å lage separate deler eller fjerne overflødig materiale.
Valget av riktig skjæreverktøy avhenger av faktorer som materialet som maskineres, ønsket finish, nødvendige dimensjoner og den spesifikke operasjonen som utføres. Det er viktig å velge riktig verktøy og vedlikeholde det riktig for å sikre effektiv og nøyaktig maskinering. Riktig verktøyvalg, sammen med riktig oppsett og justering, er avgjørende for å oppnå resultater av høy kvalitet ved dreiebenkoperasjoner.
Komponenter av et dreieverktøy
Et dreieverktøy er et presisjonsinstrument designet for å forme, kutte og fjerne materiale fra et arbeidsstykke. For å forstå hvordan det fungerer og hvordan du setter det opp, er det avgjørende å være kjent med de ulike komponentene. Her er nøkkelkomponentene til et dreieverktøy:
- Verktøyholder:Verktøyholderen er delen som fester skjæreverktøyet på plass. Den festes til dreiebenkens verktøystolpe og gir nødvendig stivhet og stabilitet for maskineringsoperasjoner. Verktøyholdere kommer i ulike design for å imøtekomme ulike typer skjæreverktøy.
- shank:Skaftet er den delen av skjæreverktøyet som passer inn i verktøyholderen. Den er vanligvis sylindrisk og klemmes fast inne i holderen. Skaftets dimensjoner og form kan variere basert på verktøytype og design.
- Skjærekant:Skjæreggen er den skarpe delen av verktøyet som kommer i kontakt med og fjerner materiale fra arbeidsstykket. Kvaliteten på skjærekanten og dens geometri påvirker skjæreytelsen og overflatefinishen betydelig. Det er viktig å opprettholde skjærekantens skarphet og presisjon.
- Sett inn:Mange moderne skjæreverktøy bruker utskiftbare innsatser, som vanligvis er laget av harde materialer som karbid eller keramikk. Disse innsatsene har skjæregeometrien og er festet i en lomme på skjæreverktøyet. De kan roteres eller skiftes ut når de blir slitt eller skadet, noe som forlenger verktøyets levetid.
- Verktøynese:Verktøynesen er selve tuppen av skjæreverktøyet der skjærekanten og innsatsen (hvis brukt) kommer sammen. Verktøynesen må være nøyaktig posisjonert og justert for presis bearbeiding. Noen skjæreverktøy for dreiebenk har en justerbar verktøyradius for bedre kontroll over verktøyytelsen.
- Verktøyflanke:Verktøyflanken er sideflaten til skjæreverktøyet som ikke er en del av skjærekanten. Riktige klaringsvinkler på verktøyflanken sikrer sponevakuering og reduserer friksjonen mellom verktøyet og arbeidsstykket.
- Verktøy rakeflate:Riveflaten er overflaten på skjæreverktøyet som vender mot arbeidsstykket. Vinkelen og tilstanden til riveflaten påvirker spondannelse og skjæreprosessens effektivitet. Rivevinkelen er et kritisk aspekt av verktøyets geometri.
- Verktøyavlastningsvinkel:Avlastningsvinkelen er vinkelen mellom verktøyflanken og verktøyets akse. Det sikrer at skjærekanten ikke gnis mot arbeidsstykket, noe som reduserer friksjon og varmeutvikling.
- Verktøyets klaringsvinkel:Klareringsvinkelen er vinkelen mellom rakeflaten og arbeidsstykkets overflate. Den lar spon flyte jevnt og forhindrer interferens mellom verktøyet og arbeidsstykket.
- Chip Breaker (hvis aktuelt):Noen skjæreverktøy, spesielt de som brukes til grovarbeid, har en sponknekker, et spor eller hakk på riveflaten. Sponbryteren hjelper til med å kontrollere spondannelse og forbedre sponevakueringen.
Riktig montering, justering og vedlikehold av disse komponentene er avgjørende for å oppnå presis og effektiv maskinering. Valget av skjæreverktøy og dets oppsett må skreddersys til den spesifikke maskineringsoperasjonen og materialet som arbeides med. Regelmessig inspeksjon og vedlikehold av skjæreverktøykomponentene er også nødvendig for å sikre konsistente resultater av høy kvalitet.
Velge riktig skjæreverktøy for jobben
Å velge riktig skjæreverktøy er en kritisk beslutning i enhver maskineringsoperasjon, siden det i stor grad påvirker kvaliteten, effektiviteten og presisjonen til arbeidet. Flere faktorer bør vurderes når du velger riktig skjæreverktøy for en spesifikk jobb. Her er en veiledning for hvordan du velger riktig skjæreverktøy for ditt maskineringsprosjekt:
1. Materiale til arbeidsstykket:
Materialet du bearbeider er en av de mest kritiske faktorene ved valg av verktøy. Ulike materialer har varierende hardhet, varmeledningsevne og sliteevne. Vurder følgende:
- Hardhet: Harde materialer som herdet stål eller keramikk krever skjæreverktøy med harde skjærekanter, for eksempel hardmetallskjær, for å tåle de høye skjærekreftene.
- Myke materialer: For mykere materialer som aluminium eller plast kan høyhastighetsstål (HSS) eller andre verktøymaterialer være tilstrekkelig.
2. Maskineringsoperasjon:
Den spesifikke operasjonen du utfører, for eksempel dreiing, fresing, boring, gjenging eller sporing, vil diktere hvilken type skjæreverktøy du trenger. Ulike verktøy er designet for ulike oppgaver, og å velge riktig sikrer optimal ytelse.
3. Skjærehastighet og matehastighet:
Bestem nødvendig skjærehastighet og matehastighet basert på materialet og maskineringsoperasjonen. Produsenter av skjæreverktøy gir anbefalinger for disse parameterne basert på verktøyets design og materialet som bearbeides. Å følge disse anbefalingene er avgjørende for å oppnå de ønskede resultatene.
4. Verktøygeometri:
Vurder geometrien til skjæreverktøyet, inkludert skråvinkelen, klaringsvinkelen og verktøyets neseradius. Verktøygeometrien skal samsvare med materialet og snitttypen. For eksempel er en positiv rakevinkel egnet for mykere materialer, mens en negativ rakevinkel er bedre for hardere materialer.
5. Arbeidsstykkets dimensjoner:
Størrelsen og dimensjonene til arbeidsstykket påvirker også valg av verktøy. Noen skjæreverktøy er bedre egnet for grovarbeid for å fjerne bulkmateriale raskt, mens andre er designet for etterbehandling for å oppnå nøyaktige dimensjoner og overflatefinish.
6. Krav til overflatefinish:
Hvis du trenger en spesifikk overflatefinish, velg et skjæreverktøy med passende geometri og skarphet. Etterbehandlingsverktøy er designet for å gi en jevnere overflatefinish, mens grovbearbeidingsverktøy er mer effektive for materialfjerning.
7. Verktøymateriale:
Valg av verktøymateriale er avgjørende. Karbid, høyhastighetsstål (HSS), keramikk og belagt verktøy har alle sine fordeler og begrensninger. Vurder faktorer som verktøyets levetid, slitestyrke og kostnadene for verktøymaterialet i din avgjørelse.
8. Kjølevæske og smøring:
Vurder om kutteoperasjonen krever kjølevæske eller smøring. Noen materialer genererer overdreven varme under bearbeiding, og bruk av riktig kjøle- eller smøremiddel kan forlenge verktøyets levetid og forbedre kutteytelsen.
9. Verktøybelegg:
Mange moderne skjæreverktøy kommer med spesialiserte belegg som TiN (Titanium Nitride) eller TiAlN (Titanium Aluminium Nitride) for å forbedre slitestyrken og redusere friksjonen. Velg et verktøy med passende belegg for din spesifikke applikasjon.
10. Kostnadshensyn:
Å balansere kostnadene for skjæreverktøyet med dets ytelse og levetid er avgjørende. Selv om premiumverktøy kan tilby lengre verktøylevetid og bedre ytelse, er det viktig å finne en balanse som stemmer overens med prosjektets budsjett.
11. Verktøyholder og maskinkompatibilitet:
Sørg for at det valgte skjæreverktøyet er kompatibelt med dreiebenken eller maskineringssenterets verktøyholdersystem. Verktøyholderen skal gi stabilitet og stivhet til skjæreverktøyet under maskineringsprosessen.
Til syvende og sist vil det riktige skjæreverktøyet for jobben avhenge av en kombinasjon av disse faktorene. Rådfør deg alltid med verktøyprodusentens anbefalinger og vurder å søke råd fra erfarne maskinister eller verktøyeksperter hvis du er usikker. Riktig verktøyvalg og oppsett er grunnleggende for å oppnå effektive og presise maskineringsresultater.
Sette opp dreiebenk-skjæreverktøyet
Å sette opp et dreieverktøy for CNC-dreiing er en systematisk prosess som involverer flere avgjørende trinn. Hvert trinn er avgjørende for å sikre at skjæreverktøyet er riktig plassert og justert, noe som til slutt fører til presis og effektiv maskinering. La oss gå gjennom prosessen trinn for trinn:
Trinn 1: Forberede dreiebenken og arbeidsstykket
Før du kan sette opp skjæreverktøyet, er det viktig å forberede både dreiebenken og arbeidsstykket:
- Sikre arbeidsstykket: Sørg for at arbeidsstykket er godt fastklemt i dreiebenkchucken eller spennhylsen. Sørg for at den roterer jevnt uten slingring eller vibrasjoner.
- Sikkerhet: Sørg for at alle sikkerhetstiltak er på plass, inkludert bruk av passende personlig verneutstyr (PPE) og riktige dreiebenkinnstillinger.
Trinn 2: Velge riktig verktøyholder
Verktøyholderen er en kritisk komponent i oppsettprosessen. Velg riktig verktøyholder basert på faktorer som type skjæreverktøy, operasjonen som utføres og dreiebenkens verktøystolpesystem.
- Match verktøyholderen til skjæreverktøyet: Sørg for at verktøyholderen er kompatibel med typen og størrelsen på skjæreverktøyet du har tenkt å bruke.
- Verktøyholders stivhet: Velg en verktøyholder som gir stabilitet og stivhet. Dette er spesielt viktig i høypresisjonsapplikasjoner.
Trinn 3: Montering av skjæreverktøyet
Montering av skjæreverktøyet innebærer å feste det i verktøyholderen og sikre at det er fast og riktig plassert:
- Sikre skjæreverktøyet: Sett skjæreverktøyet inn i verktøyholderen og stram eventuelle klemmemekanismer, som settskruer eller spennhylser. Sørg for at verktøyet holdes sikkert.
- Orientering: Kontroller at skjæreverktøyet er riktig orientert i forhold til arbeidsstykket. Verktøyet bør plasseres slik at det går i inngrep med arbeidsstykket i ønsket vinkel og dybde.
Trinn 4: Justering av verktøyhøyde og senterlinjejustering
Riktig verktøyhøyde og senterlinjejustering er avgjørende for å oppnå nøyaktige maskineringsdimensjoner:
- Verktøyhøydejustering: Juster verktøyets høyde for å justere det med dreiebenkens spindelsenterlinje. Bruk en verktøyhøydemåler eller en teststang for å stille inn verktøyet i riktig høyde.
- Midtlinjejustering: Sørg for at verktøyet er på linje med dreiebenkens spindelsenterlinje. Feiljustering kan resultere i maskinering utenfor midten, noe som påvirker delens nøyaktighet.
Trinn 5: Stille inn verktøyets neseradiuskompensasjon
For CNC-dreiing tar verktøyets neseradiuskompensasjon for geometrien til skjæreverktøyet. Dette er spesielt viktig når du bruker innleggsverktøy:
- Bestem verktøyets neseradius: Mål eller slå opp den nøyaktige neseradiusen til skjæreverktøyinnsatsen du bruker.
- Skriv inn radiusverdien: I CNC-kontrollprogramvaren, skriv inn den målte verktøyets neseradiusverdi for å sikre at maskinen kompenserer for verktøyets geometri ved maskinering.
Trinn 6: Angi verktøyforskyvninger
Verktøyforskyvninger tar hensyn til variasjoner i verktøydimensjoner og emnegeometri. De sikrer at verktøyets posisjon er nøyaktig justert for maskinering:
- Velg riktig verktøyforskyvning: Bestem riktig verktøyforskyvningsverdi basert på verktøyets geometri og maskineringsoperasjonen. Denne forskyvningsverdien kompenserer for eventuelle avvik.
- Angi offset-verdier: Legg inn de valgte offsetverdiene i CNC-kontrollprogramvaren. Disse verdiene vil instruere maskinen om hvordan den skal justere verktøyets posisjon nøyaktig.
Gjennom hele verktøyoppsettprosessen, bruk presisjonsmåleinstrumenter som mikrometer, høydemålere og måleskiver for å verifisere og finjustere verktøyjusteringen. Inspiser og vedlikehold skjæreverktøyet regelmessig for å sikre at det forblir skarpt og i god stand, siden et godt vedlikeholdt verktøy bidrar til konsistente og nøyaktige maskineringsresultater.
Riktig oppsett av dreieverktøyet i disse trinnene er avgjørende for å oppnå optimale resultater i CNC-svingoperasjoner. Presisjon og oppmerksomhet på detaljer under verktøyoppsett er nøkkelfaktorer for å produsere maskinerte deler av høy kvalitet.
Optimalisering av skjæreparametre for CNC-dreiing
Optimalisering av skjæreparametere er avgjørende for å oppnå effektive og høykvalitets CNC-dreieoperasjoner. De fire nøkkelaspektene som må vurderes ved optimalisering av skjæreparametere er hastigheter og matinger, skjæredybde, skjærevæsker og smøremidler og styring av verktøyets levetid.
1. Hastigheter og innmatinger:
- en. Kuttehastighet (overflatehastighet):Skjærehastighet, ofte referert til som overflatehastighet, er hastigheten som arbeidsstykket og skjæreverktøyet samhandler med. Den måles i overflatefot per minutt (SFM) eller meter per minutt (m/min). For å optimalisere skjærehastigheten, ta hensyn til materialet som maskineres og verktøyets materiale. Verktøy i høyhastighetsstål (HSS) har lavere anbefalte kuttehastigheter enn for eksempel karbidverktøy. Se data fra verktøyprodusenten eller maskineringshåndbøker for å bestemme anbefalte kuttehastigheter for spesifikke materialer og verktøy.
- b. Matehastighet:Matehastighet er den lineære hastigheten som skjæreverktøyet går inn i arbeidsstykket med. Den måles i tommer per omdreining (IPR) eller millimeter per omdreining (mm/omdreining). For å optimalisere matehastigheten, ta hensyn til faktorer som materialegenskaper, verktøygeometri og ønsket overflatefinish. Høyere matehastigheter er generelt mer produktive, men kan kreve kraftigere verktøy.
- c. Kutthastighet og matehastighetsforhold:Balansering av skjærehastighet og matehastighet er avgjørende for effektiv materialfjerning. En økning i skjærehastigheten tillater vanligvis en høyere matehastighet, men de to må justeres sammen for å forhindre verktøyslitasje og overoppheting.
2. Kuttdybde:
- en. Kuttdybde (DOC):Kuttedybden er avstanden skjæreverktøyet trenger inn i arbeidsstykket. Det er viktig å ta hensyn til materialet og verktøyets egenskaper. Optimaliser skjæredybden basert på materialets hardhet og verktøyets styrke og stivhet. Grunne kutt kan være nødvendig for hardere materialer, mens dypere kutt kan oppnås i mykere materialer.
- b. Aksial og radiell skjæredybde:Ved CNC-dreiing bør du vurdere både aksial (langs arbeidsstykkets lengde) og radial (over arbeidsstykkets diameter) skjæredybde. Optimale dybder for hver vil variere basert på operasjon og materiale.
3. Skjærevæsker og smøremidler:
- en. Velge riktig skjærevæske:Skjærevæsker er avgjørende for å spre varme, redusere friksjon og forbedre sponevakueringen. Velg riktig skjærevæske basert på materialet og maskineringsoperasjonen. Vannløselig kjølevæske, mineraloljebaserte eller syntetiske kjølevæsker kan foretrekkes for forskjellige materialer.
- b. Riktig bruk:Påfør skjærevæsker effektivt på skjæreområdet for å sikre tilstrekkelig smøring og kjøling. Dette kan gjøres gjennom flomkjøling, tåkesystemer eller levering av kjølevæske gjennom verktøyet, avhengig av maskinens kapasitet.
- c. Overvåking og vedlikehold:Overvåk skjærevæskenivåer, tilstand og forurensning regelmessig for å sikre at de forblir effektive. Oppretthold skjærevæskesystemer for å forhindre problemer som bakterievekst og nedbrytning.
4. Administrasjon av verktøyliv:
- en. Verktøyinspeksjon og vedlikehold:Implementer et rutinemessig verktøyinspeksjon og vedlikeholdsprogram for å sikre at verktøyene er i god stand. Sløve eller skadede verktøy kan føre til dårlig maskineringskvalitet og redusert verktøylevetid.
- b. Tidsplan for utskifting av verktøy:Etabler en tidsplan for utskifting av verktøy basert på faktorer som verktøyslitasje, maskinoppetid og produksjonskrav. Dette bidrar til å forhindre uventede verktøyfeil og opprettholder konsistent maskineringskvalitet.
- c. Optimalisering av verktøyets levetid:Noen verktøymaterialer og belegg gir lengre verktøylevetid. Vurder å bruke høyytelsesverktøy for å optimalisere verktøyets levetid og redusere produksjonsstans.
- d. Verktøybrikkekontroll:Effektiv sponkontroll, inkludert bruk av sponbrytere og riktig verktøygeometri, kan forlenge verktøyets levetid ved å redusere sponindusert slitasje.
Optimalisering av skjæreparametere i CNC-dreiing er en kontinuerlig prosess. Eksperimentering og finjustering kan være nødvendig for å finne de beste parametrene for en spesifikk applikasjon. Overvåk og juster disse parameterne regelmessig for å sikre optimal maskineringsytelse, verktøylevetid og delkvalitet. Riktig optimaliserte skjæreparametere forbedrer ikke bare maskineringseffektiviteten, men reduserer også verktøyslitasje og, til syvende og sist, produksjonskostnadene.
Feilsøking av vanlige problemer i verktøyinnstilling
Feilsøking av vanlige problemer i verktøyinnstilling er en essensiell ferdighet for maskinister og CNC-operatører. Å forstå og løse disse problemene kan bidra til å opprettholde presisjonen og kvaliteten på maskineringsoperasjoner. Her er noen vanlige problemer med verktøyinnstilling og deres løsninger:
1. Verktøyprat:
Utgave: Verktøyslingring oppstår når skjæreverktøyet vibrerer under maskineringsprosessen, noe som fører til dårlig overflatefinish, verktøyslitasje og potensiell skade på arbeidsstykket.
Løsning:
- Reduser hastighet eller øk feed: Juster skjæreparametere ved å enten redusere skjærehastigheten eller øke matehastigheten. Denne endringen kan dempe vibrasjoner og redusere skravling.
- Sjekk verktøyets stivhet: Sørg for at verktøyholderen og verktøyet er riktig sikret og at verktøyet ikke strekker seg for langt fra holderen.
- Sjekk fastspenning av arbeidsstykket: Sørg for at arbeidsstykket er godt fastklemt for å forhindre eventuelle arbeidsstykkerelaterte vibrasjoner.
- Bruk fukteteknikker: Noen maskiner kommer med funksjoner for å dempe vibrasjoner. Hvis tilgjengelig, vurder å bruke dem.
- Velg et stivere verktøy: Et mer stivt verktøy, for eksempel et med færre fløyter, kan bidra til å redusere skravling.
2. Dårlig overflatefinish:
Utgave: En dårlig overflatefinish kan skyldes problemer med verktøyoppsett eller skjæreparametere, noe som kan føre til ru eller inkonsekvente overflater på arbeidsstykket.
Løsning:
- Sjekk verktøygeometri: Sørg for at skjæreverktøyets geometri er passende for operasjonen. Et skarpt verktøy med riktig geometri er avgjørende for å oppnå en god overflatefinish.
- Optimaliser skjæreparametere: Juster skjærehastighet, matehastighet og skjæredybde for å finne den beste kombinasjonen for det spesifikke materialet og operasjonen.
- Se etter verktøyslitasje: Inspiser verktøyet for tegn på slitasje eller skade, slik som avskallede kanter. Bytt ut eller slip verktøyet etter behov.
- Bruk passende skjærevæske: Riktig smøring og kjøling kan påvirke overflatefinishen betydelig. Bruk riktig skjærevæske for materialet og driften.
- Minimer vibrasjon: Ta tak i vibrasjonsproblemer for å unngå å skape ujevnheter i overflaten.
3. Dimensjonsunøyaktigheter:
Utgave: Deler kan ha feil dimensjoner på grunn av feiljustert verktøy eller verktøyslitasje.
Løsning:
- Sjekk verktøyoppsett: Kontroller at verktøyet er riktig satt opp med riktig høyde og innretting i forhold til arbeidsstykket.
- Kalibrer maskinen: Sørg for at CNC-maskinen er riktig kalibrert og at den tolker verktøyforskyvninger og verktøydata nøyaktig.
- Juster verktøyforskyvninger: Korriger eventuelle feil i verktøyforskyvninger ved å måle verktøyet nøyaktig og angi riktige offsetverdier i CNC-kontrollen.
- Inspiser verktøyslitasje: Inspiser skjæreverktøyet regelmessig for slitasje og bytt ut eller slip det på nytt når det er nødvendig.
4. Problemer med brikkekontroll:
Utgave: Feil sponkontroll kan føre til problemer som spontilstopping, dårlig sponevakuering og skade på arbeidsstykket eller verktøyet.
Løsning:
- Velg riktig verktøygeometri: Velg et skjæreverktøy med passende sponbryter eller geometri for materialet og operasjonen.
- Optimaliser skjæreparametere: Juster matehastigheter, skjærehastigheter og skjæredybder for å optimalisere spondannelse og evakuering.
- Bruk tilstrekkelig smøring: Riktig bruk av skjærevæsker kan bidra til å smøre og lette sponevakueringen.
- Sjekk verktøyet og arbeidsstykkets justering: Sørg for at verktøyet er riktig justert med arbeidsstykket for å forhindre sponrelaterte problemer.
5. Verktøybrudd:
Utgave: Verktøybrudd kan oppstå på grunn av overdreven kraft, feil verktøyoppsett eller materialrelaterte problemer.
Løsning:
- Optimaliser skjæreparametere: Reduser skjærekreftene ved å justere parametere som matehastigheter, skjærehastigheter og skjæredybder.
- Sjekk verktøyoppsett: Sørg for at verktøyet er sikkert montert i verktøyholderen og at det er riktig justert.
- Bruk riktig verktøymateriale: Velg riktig verktøymateriale for det spesifikke materialet du bearbeider. For eksempel er karbidverktøy bedre for harde materialer.
- Inspiser for verktøyslitasje: Sjekk verktøyet regelmessig for tegn på slitasje og skift det ut før det blir for slitt og utsatt for brudd.
Å løse disse vanlige verktøyinnstillingsproblemene krever en kombinasjon av riktig opplæring, regelmessig vedlikehold og en systematisk tilnærming til feilsøking. Evnen til å diagnostisere og løse verktøyrelaterte problemer er avgjørende for å oppnå høykvalitets og effektive maskineringsresultater.
I Konklusjon
Prosessen med å sette opp og optimalisere dreiebenk-skjæreverktøy for CNC-dreiing er et avgjørende aspekt ved maskinering som i betydelig grad påvirker kvaliteten, effektiviteten og presisjonen til produksjonsprosessene. En dyp forståelse av komponentene og funksjonene til skjæreverktøy, samt faktorene som er involvert i verktøyvalg, er avgjørende for maskinister og CNC-operatører.
Riktig oppsett av et skjæreverktøy innebærer en systematisk tilnærming, fra klargjøring av dreiebenk og arbeidsstykke til valg av riktig verktøyholder, montering av verktøyet, justering av verktøyhøyde og senterlinjejustering, og konfigurering av verktøyets neseradiuskompensasjon og verktøyforskyvninger. Hvert trinn spiller en sentral rolle for å oppnå presise og effektive maskineringsresultater.
Optimalisering av skjæreparametere, inkludert hastigheter og matinger, skjæredybde, skjærevæsker og styring av verktøyets levetid, er et annet kritisk aspekt ved CNC-dreiing. Ved å velge de riktige parametrene nøye, kan maskinister øke produktiviteten, opprettholde verktøyets levetid og forbedre overflatekvaliteten.
Til slutt er det avgjørende å kunne feilsøke vanlige problemer med verktøyinnstilling, som verktøyskravling, dårlig overflatefinish, dimensjonsunøyaktigheter, sponkontrollproblemer og verktøybrudd, for å opprettholde konsistente og høykvalitets maskineringsresultater. Å identifisere disse problemene og implementere passende løsninger sikrer at maskineringsprosessen forblir jevn og effektiv.
Samlet sett gir en omfattende forståelse av dreiemaskinskjæreverktøy og deres oppsett, kombinert med evnen til å optimalisere skjæreparametere og feilsøke problemer, maskinistene i stand til å oppnå de beste resultatene i CNC-dreieoperasjoner. Kontinuerlig læring, opplæring og erfaring er nøkkelen til å foredle disse ferdighetene og sikre vellykkede maskineringsprosesser.
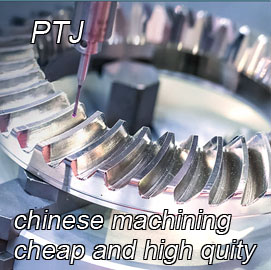
- 5 Akselmaskinering
- Cnc fresing
- CNC-dreining
- Maskineringsindustri
- Maskineringsprosess
- Overflatebehandling
- Metallbearbeiding
- Plastbearbeiding
- Pulvermetallurgisk mugg
- Die Casting
- Delegalleri
- Auto metalldeler
- Maskin deler
- LED-kjøling
- Bygningsdeler
- Mobile deler
- Medisinske deler
- Elektroniske deler
- Skreddersydd maskinering
- Sykkeldeler
- Aluminium Maskinering
- Titanbearbeiding
- Maskinering i rustfritt stål
- Kobberbearbeiding
- Messing Maskinering
- Superlegeringsbearbeiding
- Titt maskinering
- UHMW maskinering
- Unilate maskinering
- PA6 maskinering
- PPS Maskinering
- Teflon maskinering
- Inconel Maskinering
- Maskinering av verktøystål
- Mer materiale