Hvordan bearbeides høypresisjonsdeler
2023-09-22
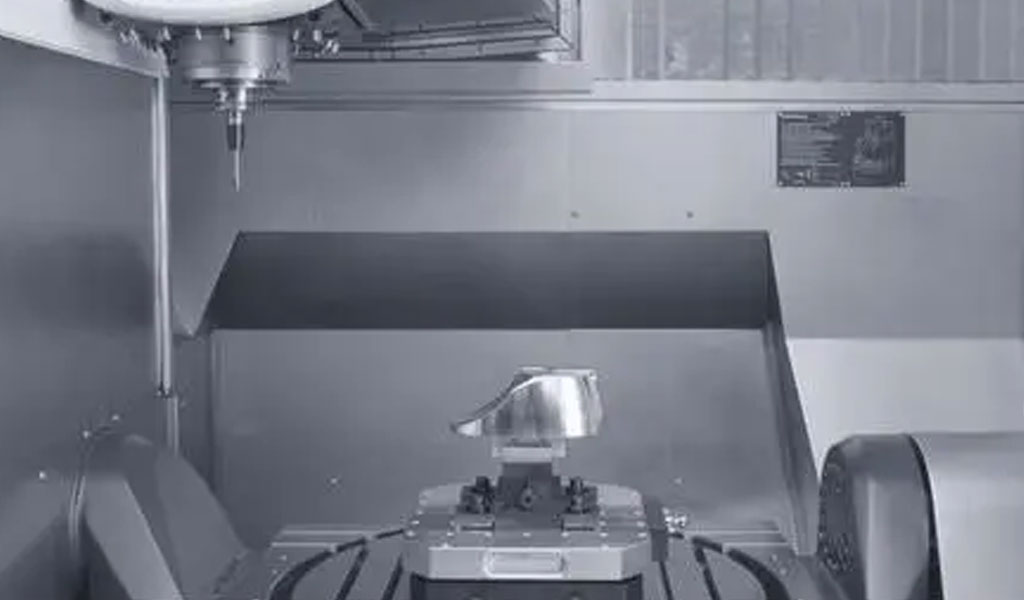
Forstå presisjonsmaskinering
Presisjonsmaskinering er en hjørnestein i moderne produksjon, ansvarlig for å produsere intrikate og nøyaktige komponenter som brukes i et bredt spekter av bransjer. For å forstå betydningen fullt ut, la oss utforske kjernekonseptene for presisjonsmaskinering, dens vitale rolle i ulike sektorer og den historiske reisen som har ført til den nåværende fortreffelighetstilstanden.A. Hva er presisjonsmaskinering?
Presisjonsmaskinering refererer til et sett med produksjonsprosesser som fjerner materiale fra et arbeidsstykke med høy grad av nøyaktighet og kontroll, noe som resulterer i fint utformede komponenter med stramme toleranser. Denne prosessen forvandler råvarer, som metaller, plast eller keramikk, til presise deler som oppfyller krevende spesifikasjoner. Nøkkelegenskapene til presisjonsmaskinering inkluderer:- Nøyaktighet: Presisjonsmaskinering sikrer at sluttproduktet samsvarer nøyaktig med den tiltenkte designen, med minimalt avvik.
- Trange toleranser: Det muliggjør produksjon av deler med ekstremt trange toleranser, noe som betyr at de ferdige komponentene holder seg tett til spesifiserte mål.
- Overlegen overflatefinish: Presisjonsmaskinering gir eksepsjonell overflatefinish, og eliminerer ofte behovet for ytterligere etterbehandlingsprosesser.
- Komplekse geometrier: Den kan skape intrikate former, konturer og funksjoner, noe som gjør den uunnværlig ved produksjon av komponenter med komplekse design.
- Repeterbarhet: Presisjon bearbeidingsprosesses er svært repeterbare, og sikrer jevn kvalitet på tvers av flere deler.
- Allsidighet: Den kan brukes på et bredt spekter av materialer, noe som gjør den egnet for ulike bransjer.
B. Viktigheten av presisjonsbearbeiding
Presisjonsmaskinering har enorm betydning i flere kritiske bransjer, og påvirker ulike aspekter av våre daglige liv. Her er noen overbevisende grunner til viktigheten:- Luftfartsindustri: I romfartssektoren er presisjonsbearbeiding uunnværlig for å lage komponenter som tåler ekstreme forhold. Flymotorer, landing utstyr, og strukturelle elementer er avhengige av presisjonsbearbeidede deler for sikkerhet og ytelse.
- Medisinsk utstyr: Medisinsk utstyr som kirurgiske instrumenter, proteser og implanterbare enheter krever presisjonsmaskinering for biokompatibilitet, nøyaktighet og pasientsikkerhet.
- Bilindustri: Presisjonsbearbeidede deler er avgjørende for bilindustrien for å sikre påliteligheten og effektiviteten til kjøretøy. Komponenter som motordeler, transmisjonssystemer og bremsemekanismer er avhengige av nøyaktig maskinering.
- Elektronikk og halvledere: Presisjonsmaskinering er sentralt i produksjonen av mikroelektroniske komponenter og halvlederenheter, der små toleranser er avgjørende for funksjonalitet.
- Energisektoren: Energiindustrien er avhengig av presisjonsmaskinering for produksjon av kritiske deler som brukes i kraftproduksjon, inkludert turbiner, generatorer og transmisjonskomponenter.
- Verktøy- og formfremstilling: Presisjonsmaskinering er avgjørende i produksjonen av verktøy og dyser, som igjen brukes til å lage utallige andre produkter.
- Consumer Electronics: Produksjonen av smarttelefoner, bærbare datamaskiner og annen forbrukerelektronikk drar nytte av presisjonsbearbeiding for å sikre elegant design og optimal funksjonalitet.
- Forskning og utvikling: Forskere og forskere er avhengige av presisjonsmaskinerte komponenter for eksperimenter, prototyper og laboratorieutstyr.
C. Historisk perspektiv
Reisen med presisjonsmaskinering går tilbake til eldgamle sivilisasjoner, der dyktige håndverkere brukte rudimentære verktøy for å forme materialer. Imidlertid var presisjonen oppnådd i disse tider begrenset sammenlignet med moderne standarder.- Tidlig presisjonsbearbeiding: Den industrielle revolusjonen på 18- og 19-tallet markerte en sentral periode i utviklingen av presisjonsmaskinering. Oppfinnelsen av verktøymaskiner, som dreiebenker og fresemaskiner, revolusjonerte produksjonen ved å muliggjøre større nøyaktighet og konsistens.
- Verdenskrig: Presisjonsmaskinering spilte en sentral rolle i andre verdenskrig, da det var avgjørende for å produsere militært utstyr med nødvendig presisjon og ensartethet. Denne epoken var vitne til fremskritt innen maskineringsteknikker og fremveksten av nye materialer.
- Fremskritt etter krigen: Etterkrigstiden så en bølge i teknologiske nyvinninger, inkludert bruk av numeriske datamaskiner (CNC). CNC-bearbeiding tillatt for automatiserte og svært presise operasjoner, og innledet en ny æra av produksjon.
- Den digitale tidsalder: Integreringen av datamaskiner og programvare i maskineringsprosesser har økt presisjonsmaskinering ytterligere. Moderne CNC-maskiner kan utføre komplekse operasjoner med uovertruffen nøyaktighet, noe som gjør dem uunnværlige i dagens produksjonslandskap.
Materialer og deres betydning
Materialer er grunnlaget for presisjonsmaskinering, og valg av riktig materiale spiller en sentral rolle i produksjonen av høypresisjonsdeler. I denne delen vil vi fordype oss i viktigheten av å velge riktige materialer, forstå betydningen av materialegenskaper og utforske de ulike faktorene som påvirker bearbeidbarheten.A. Valg av materialer
Valg av materialer i presisjonsmaskinering er en kritisk beslutning som direkte påvirker ytelsen, holdbarheten og funksjonaliteten til sluttproduktet. Produsenter må vurdere flere faktorer når de velger materialer:- Material egnethet: Materialet må være egnet for tiltenkt bruk. Ulike bransjer og applikasjoner har varierende krav, som temperaturmotstand, korrosjonsmotstand og elektrisk ledningsevne.
- Mekaniske egenskaper: Mekaniske egenskaper som strekkfasthet, hardhet og duktilitet er avgjørende. For eksempel i romfart er materialer med høy strekkfasthet foretrukket for strukturelle komponenter.
- Termiske egenskaper: Noen bruksområder krever materialer med utmerket varmeledningsevne eller motstand mot høye temperaturer. Dette er spesielt viktig i bransjer som kraftproduksjon og elektronikk.
- Korrosjon Resistance: I miljøer hvor korrosjon er et problem, foretrekkes materialer med høy motstand mot korrosjon, slik som rustfritt stål eller titan.
- Vekthensyn: Bransjer som bil og romfart prioriterer ofte lette materialer som aluminium eller karbonfiberkompositter for å redusere drivstofforbruket og forbedre ytelsen.
- Kostnadsbegrensninger: Kostnad er en vesentlig faktor i materialvalg. Høyytelsesmaterialer kan være dyre, så produsenter må finne en balanse mellom ytelse og kostnadseffektivitet.
- Overholdelse av regelverk: I bransjer som helsetjenester, må materialer oppfylle strenge regulatoriske standarder for biokompatibilitet og sikkerhet.
- Tilgjengelighet: Tilgjengeligheten av materialer og deres kilder påvirker også utvalget. Noen spesialiserte legeringer eller kompositter kan ha begrenset tilgjengelighet.
B. Materialegenskaper
Forståelse av materialenes egenskaper er avgjørende for presisjonsmaskinering. Her er noen viktige materialegenskaper og deres betydning:- Strekkfasthet: Strekkfasthet måler et materiales evne til å motstå en trekkkraft uten å gå i stykker. Det er avgjørende for strukturelle komponenter og deler som utsettes for mekanisk påkjenning.
- Hardhet: Hardhet indikerer et materiales motstand mot deformasjon og slitasje. Harde materialer er egnet for skjæreverktøy, mens mykere materialer kan være å foretrekke for visse bruksområder, som forseglinger.
- duktilitet: Duktilitet refererer til et materiales evne til å deformeres uten å gå i stykker når det utsettes for strekkspenning. Duktile materialer er lettere å forme, men er kanskje ikke egnet for applikasjoner som krever stivhet.
- Termisk ledningsevne: Materialer med høy varmeledningsevne sprer varme effektivt. Denne egenskapen er viktig i applikasjoner der temperaturkontroll er kritisk.
- Elektrisk Strømføringsevne: Elektrisk ledningsevne er essensielt i elektronikk og elektriske komponenter, der materialer må lette strømningen av elektrisitet.
- Magnetiske egenskaper: Magnetiske egenskaper er viktige i bransjer som elektromagnetikk og elektronikk, der materialer kan trenge å være ferromagnetiske eller ikke-magnetiske.
- Kjemisk motstand: Materialer må motstå kjemisk korrosjon i miljøer hvor de utsettes for syrer, baser eller andre etsende stoffer.
C. Bearbeidbarhetsfaktorer
Bearbeidbarhet refererer til hvor lett et materiale kan maskineres, kuttes eller formes. Det påvirkes av ulike faktorer, inkludert:- Materialets hardhet: Mykere materialer er generelt lettere å bearbeide, mens hardere materialer kan kreve spesialiserte verktøy og teknikker.
- Chipdannelse: Dannelse og evakuering av spon under maskinering påvirker prosessens effektivitet og overflatefinish.
- Verktøyslitasje: Ulike materialer kan forårsake varierende grad av verktøyslitasje, påvirke maskineringshastigheten og kostnadene.
- Kjølevæske og smøring: Riktig kjølevæske og smøring er avgjørende for å redusere friksjon, varme og verktøyslitasje under bearbeiding.
- Skjærehastighet: Hastigheten som skjæreverktøyet beveger seg gjennom materialet med påvirker både produktiviteten og kvaliteten på den maskinerte overflaten.
- Verktøymateriale: Valget av skjæreverktøymateriale, som karbid eller høyhastighetsstål, avhenger av materialet som maskineres.
- Skjæreparametere: Justering av skjæreparametere som matehastighet og skjæredybde kan optimere bearbeidingsprosessen for spesifikke materialer.
Maskinverktøy for presisjonsbearbeiding
Maskinverktøy er hjertet av presisjonsmaskinering, som muliggjør transformasjon av råmaterialer til høypresisjonsdeler. I denne delen vil vi utforske fire hovedtyper av maskinverktøy som brukes i presisjonsmaskinering: CNC-bearbeidingssentre, dreiemaskiner, slipemaskiner og EDM (Electrical Discharge Machining). Hver av disse maskinene spiller en unik rolle i produksjonen av presise komponenter.A. CNC-bearbeidingssentre
CNC (Computer Numerical Control) maskineringssentre er allsidige og mye brukt i presisjonsmaskinering. De er automatiserte systemer som kontrollerer bevegelsen til skjæreverktøy og arbeidsstykker med eksepsjonell presisjon. Her er en oversikt over CNC maskineringssentre og deres betydning:- Allsidighet: CNC maskineringssentre kan utføre ulike maskineringsoperasjoner, inkludert fresing, boring og tapping. Denne allsidigheten gjør det mulig å produsere komplekse deler med flere funksjoner.
- Høy presisjon: Datastyrt kontroll av CNC-maskiner sikrer presis verktøyplassering og konsistente resultater, noe som gjør dem ideelle for deler med små toleranser.
- Automatisering: CNC maskineringssentre kan operere kontinuerlig, med minimal menneskelig innblanding. Denne automatiseringen øker effektiviteten og reduserer risikoen for feil.
- Komplekse geometrier: De utmerker seg i å bearbeide intrikate former og konturer, noe som gjør dem egnet for industrier som romfart, der komplekse komponenter er vanlige.
- Repeterbare resultater: CNC-maskiner tilbyr utmerket repeterbarhet, og sikrer at hver del som produseres samsvarer med de nøyaktige spesifikasjonene til designet.
- Reduserte oppsetttider: CNC maskineringssentre kan programmeres til å bytte mellom ulike oppgaver raskt, minimere oppsetttider og øke produksjonseffektiviteten.
B. Dreiemaskiner
Dreiemaskiner brukes til å lage sylindriske deler ved å rotere et arbeidsstykke mens et skjæreverktøy fjerner materiale fra dens ytre overflate. De er avgjørende for å produsere aksels, pinner og andre komponenter med rotasjonssymmetri. Hovedpunkter om dreiemaskiner inkluderer:- Sylindriske deler: Dreiemaskiner spesialiserer seg på å produsere sylindriske eller rørformede komponenter, inkludert de med gjenger eller intrikate spor.
- Høye hastigheter: De opererer i høye hastigheter, noe som gjør dem egnet for deler som krever en jevn og nøyaktig finish.
- Enkel-akse operasjon: De fleste dreiemaskiner er enakse, med fokus på å forme den ytre overflaten av arbeidsstykket.
- Effektiv for masseproduksjon: Dreiing er svært effektivt for masseproduserende deler med minimalt materialavfall.
- Dreiebenk maskiner: Manuelle og CNC-styrte dreiemaskiner er ofte brukte dreiemaskiner, og tilbyr en rekke funksjoner.
C. Slipemaskiner
Slipemaskiner er konstruert for presis overflatebehandling og forming av harde eller slipende materialer. De er avgjørende for å oppnå ekstremt stramme toleranser og overlegen overflatefinish. Her er grunnen til at slipemaskiner er viktige:- Presisjon på mikronnivå: Slipemaskiner kan oppnå presisjon på mikronnivå, noe som gjør dem avgjørende for bruksområder som krever det høyeste nivået av nøyaktighet.
- Materialfjerning: De fjerner materiale ved slitasje, noe som muliggjør korrigering av overflatefeil og oppnår eksepsjonell glatthet.
- Verktøy og kuttersliping: I tillegg til overflatesliping finnes det spesialiserte slipemaskiner for sliping av skjæreverktøy og fremstilling av presise profiler.
- En rekke slipemetoder: Ulike typer slipemaskiner, inkludert overflateslipere, sylindriske slipemaskiner og senterløse slipemaskiner, imøtekommer ulike maskineringsbehov.
- Herdede materialer: Sliping er spesielt egnet for herdede materialer som verktøystål og keramikk, der tradisjonelle bearbeidingsmetoder kan være ineffektive.
D. EDM (Electrical Discharge Machining)
EDM, eller Electrical Discharge Machining, er en utradisjonell maskineringsprosess som bruker elektriske utladninger til å forme materialer. Den er ideell for å lage intrikate og delikate deler der tradisjonelle skjæreverktøy kan forårsake skade. Nøkkelaspekter ved EDM inkluderer:- Ingen fysisk kontakt: EDM involverer ikke direkte fysisk kontakt mellom verktøyet og arbeidsstykket, noe som minimerer risikoen for verktøyslitasje og skade på skjøre materialer.
- Høy presisjon: Den kan oppnå høy presisjon og overflatekvalitet, selv med eksepsjonelt harde materialer.
- Wire EDM og Sinker EDM: Det er to primære typer EDM-maskiner: trådskjæring EDM, som bruker en trådelektrode, og sinker EDM, som bruker en formet elektrode.
- Komplekse former: EDM kan produsere komplekse former, for eksempel dyser og former, med intrikate detaljer og fine funksjoner.
- Varmepåvirket sone: Siden EDM ikke genererer varme ved arbeidsstykket, er det egnet for varmefølsomme materialer som romfartslegeringer.
- Langsom prosess: EDM er relativt treg sammenlignet med andre maskineringsmetoder, noe som gjør den best egnet for jobber med lavt kvantum og høy presisjon.
Skjæreverktøy og verktøy
Skjæreverktøy er i forkant av presisjonsmaskinering, og fungerer som instrumentene som former og transformerer råmaterialer til høypresisjonsdeler. I denne delen vil vi utforske de ulike typene skjæreverktøy, betydningen av verktøybelegg og faktorene som påvirker verktøyets levetid og slitasje.A. Typer skjæreverktøy
Presisjonsmaskinering er avhengig av et mangfoldig utvalg av skjæreverktøy, hver designet for spesifikke oppgaver og materialer. Valget av skjæreverktøy påvirker i stor grad effektiviteten og nøyaktigheten til bearbeidingsprosessen. Her er noen vanlige typer skjæreverktøy:- End Mills: Pinnfreser er allsidige verktøy som brukes til freseoperasjoner. De har flere skjærekanter og kan fjerne materiale fra arbeidsstykket på forskjellige måter, inkludert fronting, konturering og slisser.
- Drills: Bor er designet for å lage hull i arbeidsstykker. De kommer i forskjellige former, inkludert spiralbor, senterbor og vendbare bor.
- Snu innlegg: Disse brukes i dreiemaskiner for å forme sylindriske deler. Dreieinnsatser er tilgjengelige i en rekke former og materialer for å passe til ulike bruksområder.
- Fresekutter: Fresefreser kommer i forskjellige former, for eksempel flatfreser, kulefreser og sporfresere, og brukes i fresemaskiner for å lage ulike funksjoner på arbeidsstykket.
- Reamers: Rømmere brukes til etterbehandling og dimensjonering av tidligere borede hull til nøyaktige dimensjoner. De sikrer jevne og nøyaktige hullflater.
- Taps and Dies: Disse skjæreverktøyene brukes til gjengeoperasjoner. Kraner lager innvendige gjenger, mens dyser lager utvendige gjenger.
- Slipehjul: Slipeskiver er slipeverktøy som brukes til presisjonssliping av overflater. De er tilgjengelige i forskjellige slipende materialer og kornstørrelser.
- Brosjer: Brosjer er spesialiserte verktøy som brukes til å kutte innvendige og utvendige former og profiler, for eksempel kilespor og splines.
- Forboringer og forsenker: Disse verktøyene brukes til å lage utsparinger eller avfasninger rundt hull for låss.
- Kjedelige barer: Borestenger brukes i boreoperasjoner for å forstørre eksisterende hull med presisjon.
B. Verktøybelegg
Verktøybelegg er tynne lag med materiale som påføres skjæreverktøy for å forbedre ytelsen og holdbarheten. Disse beleggene gir flere fordeler:- Redusert friksjon: Belegg som titannitrid (TiN) og titankarbonitrid (TiCN) reduserer friksjonen mellom verktøyet og arbeidsstykket, noe som fører til jevnere skjæring og lengre verktøylevetid.
- Forbedret hardhet: Belegg øker hardheten til verktøyets overflate, noe som gjør det mer motstandsdyktig mot slitasje og forlenger verktøyets levetid.
- Forbedret varmebestandighet: Belegg tåler høye temperaturer generert under bearbeiding, reduserer varmerelatert verktøyslitasje og øker skjærehastigheter.
- Anti-oppbyggingsegenskaper: Noen belegg har anti-adhesjonsegenskaper, som forhindrer oppbygging av materiale på verktøyets skjærekanter.
- Økt smøreevne: Belagte verktøy har forbedret smøreevne, reduserer behovet for overdreven kjølevæske og forbedrer sponevakueringen.
C. Verktøyets levetid og slitasje
Å forstå verktøyets levetid og slitasje er avgjørende for å optimalisere maskineringsprosesser og minimere produksjonskostnadene. Verktøyets levetid refererer til varigheten et skjæreverktøy forblir effektivt før det krever utskifting eller rekondisjonering. Flere faktorer påvirker verktøyets levetid og slitasje:- Skjærehastighet: Høyere skjærehastigheter kan føre til økt verktøyslitasje på grunn av høyere temperaturer som genereres under bearbeiding. Riktig valg av skjærehastigheter er avgjørende for å balansere verktøyets levetid og produktivitet.
- Feed Rate: Hastigheten som skjæreverktøyet går inn i arbeidsstykket med påvirker verktøyslitasjen. Høye matehastigheter kan akselerere slitasje, mens lavere matehastigheter kan forlenge verktøyets levetid.
- Skjæredybde: Kuttdybden påvirker mengden materiale som fjernes per passering. Dypere kutt kan øke verktøyslitasjen, så optimalisering av dybden er avgjørende.
- Materialets hardhet: Kutting av harde materialer kan fremskynde slitasje på verktøy. Spesialiserte verktøy og belegg brukes for å bearbeide harde materialer effektivt.
- Kjølevæske og smøring: Riktig kjølevæske og smøring bidrar til å spre varme og redusere friksjon, noe som forlenger verktøyets levetid.
- Verktøymateriale: Materialet som skjæreverktøyet er laget av påvirker slitestyrken. Materialer som karbid og keramikk gir utmerket slitestyrke.
- Verktøygeometri: Geometrien til skjæreverktøyet, inkludert skråvinkel, avlastningsvinkel og sponbryterdesign, spiller en betydelig rolle i slitasjemønstre.
- Arbeidsstykkemateriale: Materialtypen som bearbeides påvirker verktøyslitasjen. Slipende materialer kan føre til raskere verktøyslitasje.
Presisjonsbearbeidingsprosesser
Presisjonsmaskineringsprosesser er metodene der råmaterialer omdannes til høypresisjonsdeler med stramme toleranser og eksepsjonell overflatefinish. I denne delen vil vi utforske fem viktige presisjonsmaskineringsprosesser: dreiing, fresing, boring, sliping og elektrisk utladningsbearbeiding (EDM). Hver av disse prosessene tjener et unikt formål og brukes basert på de spesifikke kravene til arbeidsstykket.A. Snuing
Dreiing er en maskineringsprosess som primært brukes til å forme sylindriske deler. Det innebærer å rotere et arbeidsstykke mens et enkeltpunkts skjæreverktøy fjerner materiale fra den ytre overflaten. Her er de viktigste aspektene ved dreiing:- Sylindriske deler: Dreiing er ideell for å produsere sylindriske komponenter som aksler, pinner og hylser.
- Rotasjonssymmetri: Den er godt egnet for deler som krever rotasjonssymmetri, da arbeidsstykket roterer på en dreiebenk mens skjæreverktøyet former det.
- Ulike operasjoner: Dreiing kan utføre ulike operasjoner, inkludert vending, vending (redusere diameteren), konisk dreiing og gjenging.
- Enkeltpunktsskjæring: Et enkelt skjæreverktøy fjerner materiale i en kontinuerlig bevegelse, noe som resulterer i effektiv materialfjerning.
- Dreiebenk maskiner: Både manuelle og CNC-styrte dreiebenkmaskiner brukes ofte til dreieoperasjoner.
B. Fresing
Fresing er en allsidig presisjonsbearbeidingsprosess som bruker flerpunktsskjæreverktøy for å fjerne materiale fra et arbeidsstykke. Den er godt egnet for å lage et bredt spekter av former og funksjoner. Nøkkelaspekter ved fresing inkluderer:- Allsidighet: Fresing kan produsere flate overflater, spor, lommer og komplekse konturer. Den brukes til både 2D og 3D maskinering.
- Flerpunktsskjæring: Flere skjærekanter på verktøyet samhandler med arbeidsstykket samtidig, noe som muliggjør effektiv fjerning av materiale.
- Typer fresing: Fresing kan utføres ved hjelp av ulike typer kuttere, inkludert endefreser, planfreser og kulefreser.
- CNC Maskineringssentre: CNC-styrte fresemaskiner gir presis kontroll over verktøybevegelser og er mye brukt i moderne maskinering.
- Høye hastigheter: Fresing kan utføres ved høye hastigheter, noe som muliggjør effektiv produksjon.
C. Boring
Boring er en presisjonsbearbeidingsprosess som brukes til å lage hull i arbeidsstykker. Det er en grunnleggende operasjon i ulike bransjer. Nøkkelaspekter ved boring inkluderer:- Hulloppretting: Boremaskiner bruker spesialiserte verktøy kalt bor for å fjerne materiale og lage hull med spesifikke diametre.
- Typer øvelser: Ulike typer øvelser er tilgjengelige, inkludert spiralbor, senterbor og vendebor, hver designet for spesifikke bruksområder.
- Nøyaktighet: Nøyaktig posisjonering og justering er avgjørende ved boring for å sikre at hull lages med nøyaktighet.
- Hastighet og matehastighet: Boreparametere som rotasjonshastighet og matehastighet er kritiske for å oppnå ønskede hulldimensjoner.
- Kjølevæske og smøring: Riktig kjølevæske og smøring brukes til å spre varme og redusere friksjon under boring.
D. Sliping
Sliping er en presisjonsbearbeidingsprosess som bruker slipeskiver for å fjerne materiale og oppnå ekstremt stramme toleranser og overflatefinish. Nøkkelaspekter ved sliping inkluderer:- Eksepsjonell presisjon: Sliping kan oppnå presisjon på mikronnivå, noe som gjør den ideell for applikasjoner som krever den høyeste nøyaktigheten.
- Overflatebehandling: Den produserer overlegen overflatefinish, og eliminerer ofte behovet for ytterligere etterbehandlingsprosesser.
- materialer: Sliping er egnet for harde og slipende materialer, inkludert herdet stål, keramikk og karbider.
- En rekke slipemetoder: Ulike typer slipemaskiner, som overflateslipere, sylindriske slipemaskiner og senterløse slipemaskiner, imøtekommer ulike maskineringsbehov.
- Kjølevæske: Riktig kjølevæske er avgjørende ved sliping for å forhindre overoppheting og opprettholde hjulets integritet.
E. Maskinering av elektrisk utladning (EDM)
EDM, eller Electrical Discharge Machining, er en utradisjonell presisjonsmaskinprosess som bruker elektriske utladninger for å fjerne materiale. Den er spesielt egnet for maskinering av komplekse og intrikate former, samt harde og varmebestandige materialer. Nøkkelaspekter ved EDM inkluderer:- Bearbeiding uten kontakt: EDM involverer ikke direkte kontakt mellom verktøyet og arbeidsstykket, noe som reduserer risikoen for verktøyslitasje og skade.
- Høy presisjon: EDM kan oppnå høy presisjon, noe som gjør den egnet for applikasjoner der trange toleranser er avgjørende.
- Komplekse former: Den utmerker seg i å bearbeide komplekse former, matriser, støpeformer og komponenter med fine detaljer.
- Wire EDM og Sinker EDM: Det er to primære typer EDM-maskiner: wire EDM, som bruker en wire-elektrode, og sinker EDM, som bruker en formet elektrode.
- Langsom prosess: EDM er relativt treg sammenlignet med andre maskineringsmetoder, noe som gjør den best egnet for jobber med lavt kvantum og høy presisjon.
Toleranser og kvalitetskontroll
Presisjonsmaskinering krever grundig oppmerksomhet på detaljer og en streng forpliktelse til kvalitetskontroll for å sikre at deler oppfyller de spesifiserte standardene. I denne delen vil vi utforske tre kritiske aspekter ved kvalitetskontroll i presisjonsmaskinering: Geometrisk dimensjonering og toleranse (GD&T), Statistisk prosesskontroll (SPC) og kvalitetssikring.A. Geometrisk dimensjonering og toleranse (GD&T)
Geometrisk dimensjonering og toleranse, ofte forkortet som GD&T, er et system som brukes til å definere og kommunisere de tillatte variasjonene i størrelse, form, orientering og plassering av funksjoner på en del. GD&T er avgjørende for presisjonsmaskinering av følgende grunner:- Nøyaktig kommunikasjon: GD&T tilbyr et standardisert språk for ingeniører, designere og maskinister for å kommunisere designhensikt og dimensjonskrav nøyaktig.
- Toleranseavklaring: Det hjelper med å definere akseptable variasjoner i kritiske dimensjoner, og sikrer at alle interessenter forstår de tillatte avvikene.
- Forbedret kvalitet: GD&T fremmer forbedret kvalitet ved å redusere tvetydighet i designspesifikasjoner, og minimere risikoen for feil under maskinering.
- Kostnadseffektivitet: Tydelige GD&T-spesifikasjoner kan føre til reduserte produksjonskostnader, siden det er mindre sannsynlig at deler blir kassert eller krever omarbeid på grunn av misforståelser eller feiltolkninger.
- Kompleks geometri: Den er spesielt nyttig for deler med komplekse geometrier, og sikrer at alle funksjoner er produsert etter de ønskede spesifikasjonene.
B. Statistisk prosesskontroll (SPC)
Statistical Process Control (SPC) er en kvalitetskontrollmetodikk som bruker statistiske teknikker for å overvåke og kontrollere maskineringsprosessen. SPC er avgjørende for presisjonsmaskinering av følgende grunner:- Prosessovervåking: SPC hjelper til med å overvåke maskineringsprosesser i sanntid, identifisere variasjoner eller avvik fra ønskede parametere.
- Tidlig oppdagelse av problemer: Ved å overvåke prosessen kontinuerlig, gir SPC mulighet for tidlig oppdagelse av problemer som kan føre til deler som ikke er spesifisert, noe som reduserer avfall og omarbeiding.
- Datadrevet beslutningstaking: SPC er avhengig av data og statistisk analyse for å ta informerte beslutninger om prosessjusteringer, og sikrer at maskineringsprosessen forblir innenfor akseptable grenser.
- Forbedret konsistens: SPC fremmer prosesskonsistens og reduserer sannsynligheten for å produsere deler som ikke samsvarer.
- Redusert skrot og omarbeid: Ved å identifisere og adressere prosessvariasjoner raskt, minimerer SPC produksjonen av defekte deler, og reduserer skrot- og omarbeidskostnader.
C. Kvalitetssikring i presisjonsbearbeiding
Kvalitetssikring innen presisjonsmaskinering omfatter en omfattende tilnærming for å sikre at produserte deler oppfyller eller overgår spesifiserte kvalitetsstandarder. Det involverer ulike elementer, inkludert:- Prosessdokumentasjon: Detaljert dokumentasjon av maskineringsprosesser, inkludert standard driftsprosedyrer (SOPs) og arbeidsinstruksjoner, sikrer at hvert trinn utføres konsekvent.
- Inspeksjon og måling: Streng inspeksjon og måling ved bruk av presisjonsinstrumenter og metrologiske teknikker bekrefter at deler samsvarer med spesifiserte toleranser og kvalitetsstandarder.
- Kalibrering: Regelmessig kalibrering av maskineringsutstyr og måleinstrumenter er avgjørende for å opprettholde nøyaktighet og sporbarhet.
- Materialverifisering: Verifikasjon av materialegenskaper, sammensetning og kvalitet er avgjørende for å sikre at materialet som brukes oppfyller designkravene.
- Ansattes opplæring: Opplærings- og kompetanseutviklingsprogrammer for maskinister og kvalitetskontrollpersonell sikrer at de er dyktige i sine roller og ansvar.
- Årsaksanalyse: Når deler som ikke er i samsvar blir identifisert, utføres rotårsaksanalyse for å fastslå kilden til problemet og implementere korrigerende tiltak.
- Kontinuerlig Forbedring: En kultur med kontinuerlig forbedring fremmer innovasjon og driver kontinuerlig forbedringer i maskineringsprosesser og kvalitetskontrollprosedyrer.
- Tilbakemeldinger fra kunder: Innsamling og analyse av tilbakemeldinger fra kunder hjelper til med å identifisere områder for forbedring og justerer maskineringsprosesser med kundenes forventninger.
konklusjonen
A. Kunsten og vitenskapen om presisjonsmaskinering
Presisjonsmaskinering står i skjæringspunktet mellom kunst og vitenskap, der kreativitet, dyktighet og innovasjon samles for å produsere høypresisjonsdeler som driver industri og former den moderne verden. Det er både en kunstform som krever håndverket og ekspertisen til maskinister som forvandler råvarer til verk av ingeniørkunst, og en vitenskap som er avhengig av banebrytende teknologi, materialvitenskap og avanserte prosesser for å oppnå enestående presisjon. Reisen med presisjonsmaskinering tar oss gjennom forståelsen av materialer og deres egenskaper, mestring av skjærende verktøy og maskineri, og grundig kontroll av prosesser og toleranser. Det omfatter språket for geometrisk dimensjonering og toleranse, årvåkenhet til statistisk prosesskontroll og forpliktelsen til kvalitetssikring. Presisjonsmaskinering spiller en sentral rolle i forskjellige bransjer, fra romfart og bilindustri til medisinsk utstyr og elektronikk, og former alt fra flymotorer til kunstige ledd og mikrobrikker. Det gjør det mulig å lage komponenter som fungerer med uovertruffen nøyaktighet og pålitelighet, og ofte flytter grensene for hva som er mulig.B. Siste tanker
Når vi avslutter denne utforskningen av presisjonsmaskinering, er det klart at dette feltet ikke bare handler om å lage deler; det handler om å skape muligheter. Jakten på presisjon driver innovasjon, og flytter grensene for hva som kan oppnås. Enten det er det delikate håndverket som kreves for å lage en klokkes intrikate gir eller den avanserte teknologien som trengs for å produsere komplekse fly- og romfartskomponenter, er presisjonsbearbeiding kjernen i det hele. Fremtiden for presisjonsmaskinering er fylt med løfter. Fremskritt innen materialvitenskap, automasjon og digitale teknologier fortsetter å omforme landskapet. Miniatyrisering, 3D-utskrift og bærekraftig produksjonspraksis blir stadig mer fremtredende, og innleder nye horisonter for industrien. I en verden hvor presisjon er viktigere enn noen gang, er presisjonsbearbeiding fortsatt en uunnværlig grunnpilar i moderne ingeniørkunst. Det er et vitnesbyrd om menneskelig oppfinnsomhet og vår urokkelige streben etter fortreffelighet i alle fasetter av produksjon. Etter hvert som etterspørselen etter høyere presisjon og mer intrikate komponenter vokser, vil presisjonsmaskinering fortsette å utvikle seg, og møte morgendagens utfordringer med samme dedikasjon og presisjon som har definert den i århundrer.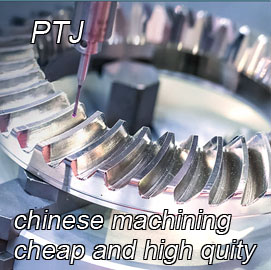
Våre tjenester
- 5 Akselmaskinering
- Cnc fresing
- CNC-dreining
- Maskineringsindustri
- Maskineringsprosess
- Overflatebehandling
- Metallbearbeiding
- Plastbearbeiding
- Pulvermetallurgisk mugg
- Die Casting
- Delegalleri
Casestudier
- Auto metalldeler
- Maskin deler
- LED-kjøling
- Bygningsdeler
- Mobile deler
- Medisinske deler
- Elektroniske deler
- Skreddersydd maskinering
- Sykkeldeler
Materialliste
- Aluminium Maskinering
- Titanbearbeiding
- Maskinering i rustfritt stål
- Kobberbearbeiding
- Messing Maskinering
- Superlegeringsbearbeiding
- Titt maskinering
- UHMW maskinering
- Unilate maskinering
- PA6 maskinering
- PPS Maskinering
- Teflon maskinering
- Inconel Maskinering
- Maskinering av verktøystål
- Mer materiale
Delegalleri